
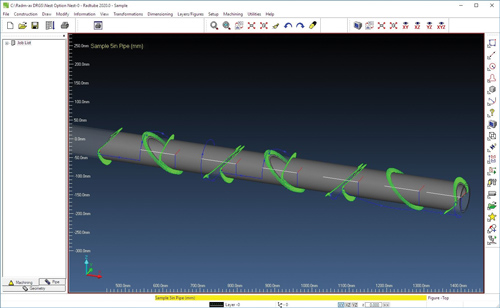
Why do CAD systems have these tolerance problems? The 64-bit mathematical precision of modern PCs is often not quite enough to calculate the shape of the NURBS curves as accurately as is necessary-particularly on models that are physically big, with fine details. The model will often come in as a whole bunch of individual surface patches, which you then need to fiddle with, to see if you can get the program to stitch them into a solid. All too often, when translating files from one system to another, the receiving system balks on some of the tolerances, and creates models with holes or gaps. The biggest problem in CAD interoperability is that different systems, handle tolerances differently. If the sewing has too many gaps, the suit will leak.Īdmittedly, this is a simplistic analogy, but it’s good enough. If the sewing is high quality, the suit will be water tight. Think of a B-rep as being like a scuba diver’s wet suit, sewn together out of individual pieces. Parts are either parametrically or explicitly defined, but in either case, their topology is defined by a boundary representation (B-rep) solid model, made up of trimmed NURBS (non-uniform rational B-spine) surfaces. Under those are parts, and separately, drawings. Modern 3D mechanical CAD systems, as a rule, all use similar data representations. Here, Kubotek Validation Tool shows the differences between an authority model, and a translated model.
